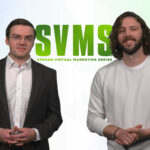
A longtime observer of Toyota’s factories contends there’s little evidence that the company’s overall standards are slipping
By Jeffrey Liker
Liker is Professor of Industrial and Operations Engineering at the University of Michigan.
I have been visiting, studying, and analyzing Toyota for 25 years in Japan, the U.S., Europe, and other countries. I have written six books about Toyota (TM) and many articles, and my students have written PhD dissertations about various aspects of the company. One of my PhD students just successfully defended a thesis on how most of the auto manufacturers, including Toyota, work with their suppliers. His data show Toyota is head and shoulders the best customer to work with on the technical details of designing, prototyping, and testing brakes.
Before all of the recent negative news—about unintended acceleration, recalls of millions of vehicles, and a shutdown of U.S. production—I was working on a book extolling the virtues of this great company, which was using the recession to retain employees, not lay them off, and teach them kaizen (the Japanese philosophy of continuous improvement).
So what happened that is causing the media to write off 60 years of progress in a company that has become a model of operational excellence? It seems to me that the inferences about Toyota’s quality problems are emotional and have little to do with actual facts.
Those facts are:
—Carpets that are not clipped down, particularly all-weather rubber carpets sold by dealers, can slide around and jam the gas pedal. This can be a problem in every car—that is why they have clips on the driver’s side to hold the carpet in place. If you clip down your carpet, it is perfectly safe. In Toyota’s case, there was one documented car crash killing four people, involving a Lexus that a dealer gave out as a loaner car. The dealer threw in an all-weather carpet without fastening it down. It trapped the pedal. The driver got into an accident and the car caught fire. The rubber mat was fused to the pedal, so it was clear what had happened.
Toyota has an extraordinary response to this incident of carpets, including cutting the size of the gas pedal for existing cars and then designing a software fix that will cause pressure on the brake to override the gas pedal and cut off the gas. It is a sophisticated piece of software that is embedded in a computer chip in the engine and has to be programmed differently for different car models and engines. All that is highly time-consuming, and it will take a while to get it into all Toyota cars.
—Sticky pedals. Apparently this is caused by an interaction between the material of one part of the pedal, as made in one plant by CTS (CTS), an automotive supplier, and humidity and wear of a part over time. It is a metal part called a shift lever. CTS uses a different material than Denso, Toyota’s other supplier of gas pedals. This is a rare problem in terms of number of problems per one million vehicles but Toyota dealers documented cases of sticky pedals. If you push down the brake firmly, the brake will work fine at slowing down and stopping the car. Apparently pedal wear can also cause problems like this in other cars, but Toyota had a series of reported cases by its customers.
Toyota has a replacement pedal in production at CTS already and has suspended U.S. production of eight models until the new pedals are ready. It still needs to find a fix for the millions of cars out on the road. That fix is expected to be days away, not weeks.
These are the two problems that led to the recall of more than 6 million vehicles and the shutdown of some factories. Is it enough to lead some in the media to suggest there’s been a significant change in quality for the whole company? To me that seems like a poor generalization. The design decision on the gas pedal was made five to 10 years ago, working with a supplier, and it passed all of the tests at the time. What does that really have to do with the rest of the company today?
SIGNS OF STRENGTH
I personally have toured Toyota plants and been in their engineering offices in the past year. Unlike many competitors, Toyota had no involuntary layoffs through the recession and had enough extra people during the slowdown to focus intensely on quality and safety. In some plants, 40% of workers who were not needed for production were paid full-time to relearn its famous production system and attack problems in the plant with a vengeance.
In its Georgetown (Ky.) plant alone, Toyota reduced defects found in final inspection by more than 40%, thanks to the ideas of workers on the line. And this plant—which makes the Camry—was already producing some of the best quality in the country. In 2009, 10 of the coveted JD Power initial quality awards for the best vehicles in a segment went to Toyota or its Lexus unit—more than any other automaker.
I come away in awe every time I visit a Toyota facility. It does not do justice to the hundreds of thousands of people in Toyota engineering and manufacturing and the supply base to leap to conclusions based on such thin evidence. Clearly it’s no small thing when a company shutters factories that produce its best-selling products. But it seems to me that the inferences about a wider quality problem at Toyota are not based on actual facts.
http://www.businessweek.com/bwdaily/dnflash/content/jan2010/db20100128_907800.htm
Posted
John Paul Strong
John Paul Strong combines his two decades of automotive marketing experience with a team of more than 150 professionals as owner and CEO of Strong Automotive.